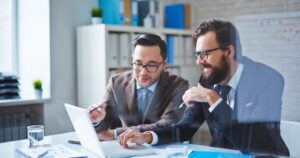
Business Intelligence 101: Navigating The Data Landscape
In the fierce global competition where competitors have access to comparable manufacturing technologies and offer similar products, high-performance business processes built on a foundation of data have become a key differentiator.